The 8-Second Trick For Alcast Company
The 8-Second Trick For Alcast Company
Blog Article
All About Alcast Company
Table of ContentsThe Ultimate Guide To Alcast CompanyAlcast Company Things To Know Before You Get ThisUnknown Facts About Alcast CompanyThings about Alcast CompanyAll about Alcast CompanyOur Alcast Company Ideas
The subtle distinction hinges on the chemical web content. Chemical Comparison of Cast Aluminum Alloys Silicon promotes castability by lowering the alloy's melting temperature and boosting fluidness during spreading. It plays a vital duty in enabling elaborate mold and mildews to be loaded properly. Furthermore, silicon adds to the alloy's strength and use resistance, making it beneficial in applications where sturdiness is important, such as automobile parts and engine elements.It also improves the machinability of the alloy, making it simpler to refine right into ended up products. In this method, iron contributes to the total workability of light weight aluminum alloys.
Manganese adds to the toughness of aluminum alloys and enhances workability (aluminum foundry). It is typically used in wrought light weight aluminum items like sheets, extrusions, and accounts. The existence of manganese aids in the alloy's formability and resistance to splitting during construction processes. Magnesium is a light-weight aspect that offers toughness and influence resistance to light weight aluminum alloys.
The 10-Minute Rule for Alcast Company
It permits the manufacturing of lightweight parts with outstanding mechanical residential or commercial properties. Zinc enhances the castability of aluminum alloys and helps control the solidification procedure throughout casting. It boosts the alloy's strength and hardness. It is often located in applications where elaborate forms and great information are essential, such as attractive castings and certain auto parts.
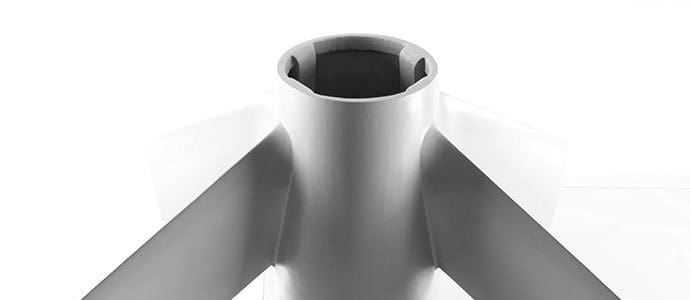
The key thermal conductivity, tensile stamina, yield toughness, and elongation differ. Among the above alloys, A356 has the highest thermal conductivity, and A380 and ADC12 have the lowest.
How Alcast Company can Save You Time, Stress, and Money.
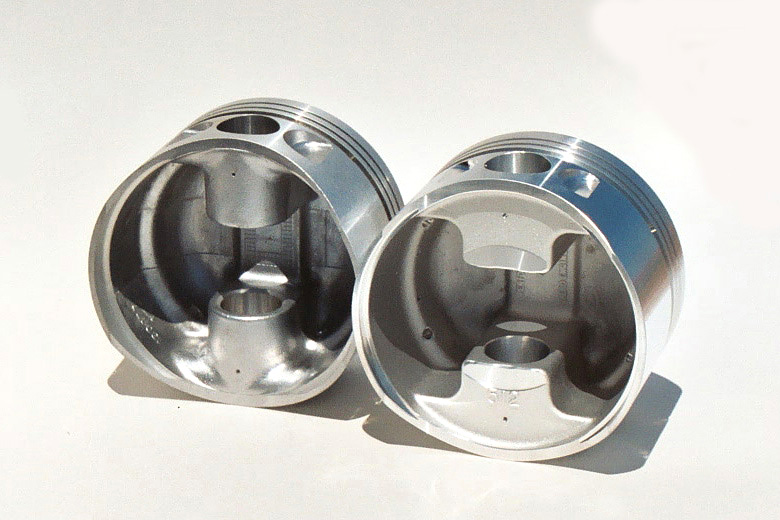
In precision casting, 6063 is appropriate for applications where complex geometries and premium surface finishes are critical. Examples include telecommunication enclosures, where the alloy's superior formability enables sleek and aesthetically pleasing designs while keeping architectural stability. In the Lights Solutions industry, precision-cast 6063 parts create sophisticated and efficient lights fixtures that require elaborate forms and good thermal performance.
It leads to a better surface finish and far better corrosion resistance in A360. Additionally, the A360 shows exceptional elongation, making it excellent for complex and thin-walled parts. In accuracy spreading applications, A360 is well-suited for industries such as Consumer Electronics, Telecommunication, and Power Devices. Its enhanced fluidity enables intricate, high-precision components like smartphone cases and interaction tool housings.
The Basic Principles Of Alcast Company
Its distinct residential properties make A360 a useful selection for precision spreading in these markets, find out here now improving product resilience and high quality. Aluminum alloy 380, or A380, is a commonly utilized casting alloy with a number of distinct characteristics. It provides superb castability, making it an ideal option for precision spreading. A380 displays good fluidity when molten, making sure intricate and comprehensive mold and mildews are accurately replicated.
In precision casting, aluminum 413 radiates in the Consumer Electronics and Power Equipment markets. This alloy's premium rust resistance makes it an outstanding option for outside applications, ensuring lasting, durable items in the stated sectors.
Alcast Company - The Facts
When you have actually made a decision that the light weight aluminum die casting process appropriates for your task, a critical next action is choosing one of the most suitable alloy. The light weight aluminum alloy you choose will significantly impact both the spreading procedure and the residential properties of the final item. Because of this, you should make your choice very carefully and take an educated approach.
Figuring out the most appropriate aluminum alloy for your application will certainly mean weighing a broad range of features. These comparative alloy attributes follow the North American Die Casting Organization's standards, and we've separated them right into 2 categories. The initial classification addresses alloy features that affect the manufacturing process. The 2nd covers attributes affecting the residential or commercial properties of the end product.
What Does Alcast Company Mean?
The alloy you choose for die spreading directly impacts a number of aspects of the casting procedure, like how very easy the alloy is to collaborate with and if it is prone to casting problems. Hot cracking, also called solidification splitting, is a common die casting flaw for light weight aluminum alloys that can result in interior or surface-level rips or splits.
Certain aluminum alloys are a lot more at risk to warm splitting than others, and your selection should consider this. An additional usual flaw found in the die spreading of aluminum is die soldering, which is when the actors stays with the die wall surfaces and makes ejection tough. It can damage both the cast and the die, so you should search for alloys with high anti-soldering properties.
Corrosion resistance, which is already a significant feature of light weight aluminum, can vary substantially from alloy to alloy and is an essential characteristic to take into consideration relying on the ecological conditions your product will certainly be subjected to (aluminum casting company). Wear resistance is one more residential or commercial property commonly sought in aluminum products and can set apart some alloys
Report this page